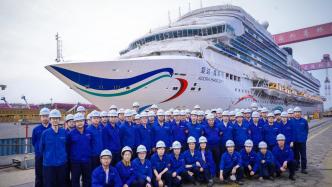

The large cruise ship construction management team of the Cruise Project Department of Shanghai Waigaoqiao Shipbuilding Co., Ltd. and the first domestically-produced large cruise ship "Aida Magic City".
As an important part of the Made in China national brand, large cruise ship projects are a concentrated reflection of my country's industrial and technological strength in the new era, and are also a national business card that effectively promotes international cultural exchanges and showcases the image of a great power. In 2023, the successful delivery of the first domestically-made large cruise ship "Aida·Modu" not only filled the gap in the shipbuilding type of China's shipbuilding industry, promoted the transformation and upgrading of the shipbuilding industry, but also further enriched the path to achieve the national marine strategy. Large cruise ship projects have become an effective carrier and a wonderful epitome of China's high-quality economic development.
“I run hard just to catch up with myself who was once highly expected of me.”
Nie Kai's signature on WeChat sounds like a young person describing the important process of his growth.
He is the secretary of the Youth League branch of the cruise project of Shanghai Waigaoqiao Shipbuilding Co., Ltd.
There is an extremely beautiful photo in his WeChat Moments: blue sea, blue sky, towering green mountains, and the main body of the picture is a bright white cruise ship.
Cruise ships are five-star hotels floating on the sea. Previously, China had never been able to enter this high-end market.
"It's not easy to make any mega project, and it's especially difficult to make the first domestically made ship," said Ma Yulin, secretary of the Youth League Committee of Shanghai Waigaoqiao Shipbuilding Co., Ltd.
Nie Kai and Ma Yulin were both very young, but together with their friends, they accomplished something big.
As the No. 1 project of China State Shipbuilding Corporation to implement the important instructions of General Secretary Xi Jinping, implement national strategies, and promote high-quality development, the first large cruise ship made in China was born, set off, and sailed in their hands. From then on, the world cruise market had Chinese presence.
The cruise ship has more than 150,000 design drawings, weighs 2.1 tons, and the number of parts in the entire ship is as high as 25 million... Filling the gap, high-end products, and transformation and development.
Shanghai Waigaoqiao Shipbuilding Co., Ltd. has added a new type of ship to its long list of deliveries.
This is an entry ticket for China to enter the high-end market of large cruise ships. Considering the upstream and downstream industrial chains driven by it and the possible "blowout" of the cruise tourism market, its economic value is immeasurable.
On November 4, 2023, the first large cruise ship built in China was officially named and delivered.
On the evening of December 31, 2023, President Xi Jinping also mentioned in his New Year’s message that “the domestically-made large cruise ship completed its sea trial.”
Next, large cruise ship No. 2, large cruise ship No. 3...
Behind this outstanding achievement is the wisdom, strength and responsibility of young people.
In order to ensure the smooth launching, sea trials, naming and delivery of the first domestically-made large cruise ship, the "Jingfeng Contribution Action" (abbreviated as "Jingfeng") team and the construction management youth commando of the first domestically-made large cruise ship were established in early 2023. This young team with an average age of less than 35 years old shouldered the heavy responsibility given by the times for a common goal of "picking the last pearl of China's shipbuilding industry". The team is responsible for the management of the construction process of the cruise ship in the "decisive year", and has achieved fruitful results in technological innovation and management improvement, which jointly promoted the successful delivery and operation of the first cruise ship.
The "Elite Contribution Action" is a youth job contribution action carried out by the Shanghai Economic and Information Technology System around the "major issues of the country" and "the key issues of the city", focusing on major national strategic tasks and the key points of Shanghai's high-quality industrial development. Starting from 2023, it will guide and support young people in the industry to serve the overall situation and lead young people in the system to carry out around the central work.
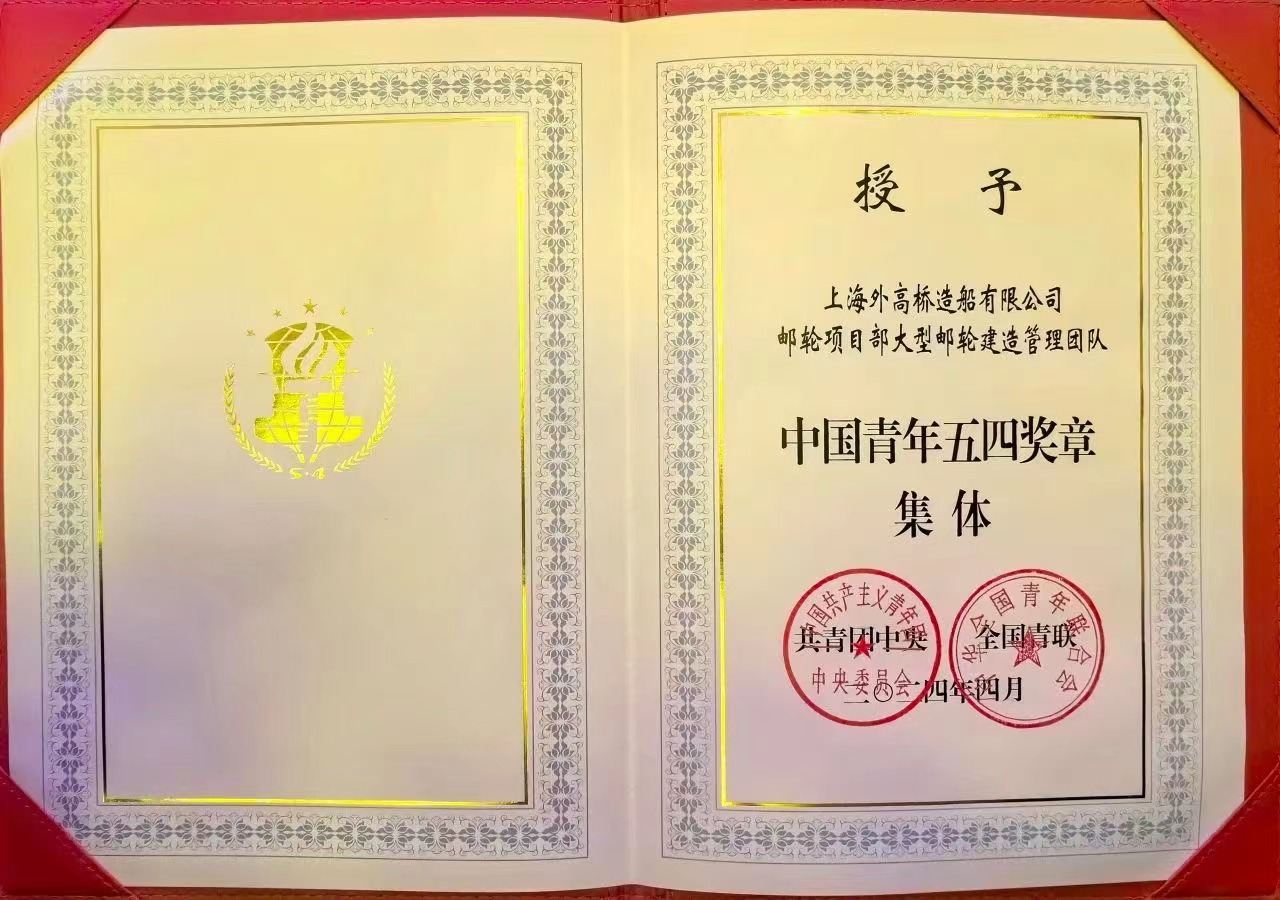
The large cruise ship construction management team of the Cruise Project Department of Shanghai Waigaoqiao Shipbuilding Co., Ltd. won the 28th "China Youth May Fourth Medal Group".
In May 2024, the large cruise ship construction management team of the Cruise Project Department of Shanghai Waigaoqiao Shipbuilding Co., Ltd. won the 28th "China Youth May Fourth Medal Group" and was the only group in Shanghai to receive this honor in 2024.
"A grand event of youth! Behind every 'highlight moment' there is a story of struggle. I am young and I will take responsibility!" After receiving the award, Ma Yulin wrote on WeChat Moments.
The problem of "No. 1": huge system engineering + three core problems
Ma Yulin said that in Europe and the United States, cruises are already a very popular way of traveling, but in China, people have not heard much about them in the past decade or so, or in recent years, because before that, cruise tourism in China was still in its infancy.
After eight years of scientific research and five years of design and construction, it was originally scheduled to be delivered by the end of 2023. However, both Nie Kai and Ma Yulin said: "At that time, we were also hesitant about whether it could be delivered by the end of 2023."
Due to the epidemic and other reasons, as of early June 2022, there is still a lot of work to be completed. In order to deliver on schedule, Waigaoqiao Shipyard has formulated a "four 120-day" work plan for the cruise project.
"We did a preliminary statistics and found that there were more than 360 first-tier suppliers, nearly 1,000 second-tier supporting enterprises, and more than 5,000 engineers and technicians from more than 30 countries around the world coordinating and linking up." Nie Kai said, "We belong to a department similar to the command center. We gradually build a multi-center, distributed and iterative cruise engineering organization and management model. This is completely different from the model we used to build other ships. In the past, a single ship supervisor was assigned to a ship, and basically all problems could be coordinated and resolved. Cruise ships are not like this. Moreover, they are long, more than 300 meters, and are managed in a grid-like manner. Deck managers and other regional production managers are divided to do balance and coordination."
For a cruise ship to be delivered smoothly, there are at least three core problems to be solved: one is weight and center of gravity control, the second is safe return to port, and the third is vibration and noise.
In terms of weight control, Nie Kai introduced that if it exceeds the limit by too much, it would violate the regulations and the ship owner might not want the ship.
He said that the ship sections were placed in the factory, and then assembled into a large piece, called the master section. The master section was moved to the dock for construction and then built into the entire ship. "One of the control points is how to weigh it at each stage and figure out the weight of each part. In order to achieve the original design goal, we still spent a lot of time and energy, including purchasing a lot of weighing equipment."
The second difficulty is safe return to port. Nie Kai introduced that safe return to port actually means that within the accident limit of fire or flooding, the ship can rely on its own power to return to the nearest port, and the safe area on board can meet the basic life needs of passengers and crew. If the fire accident limit is exceeded, but the fire does not exceed one main vertical zone, a certain number of systems are required to be available for 3 hours for orderly evacuation. The above requirements set a total of three accident scenarios: flooding of a single watertight compartment; fire within the accident limit; fire exceeding the accident limit but not exceeding one main vertical zone.
"There are more than 5,000 passengers on our ship, and with the staff there are probably more than 6,000 people. Once so many passengers are involved, their safety must be guaranteed." Nie Kai said that the current system is a "1+1" redundant system.
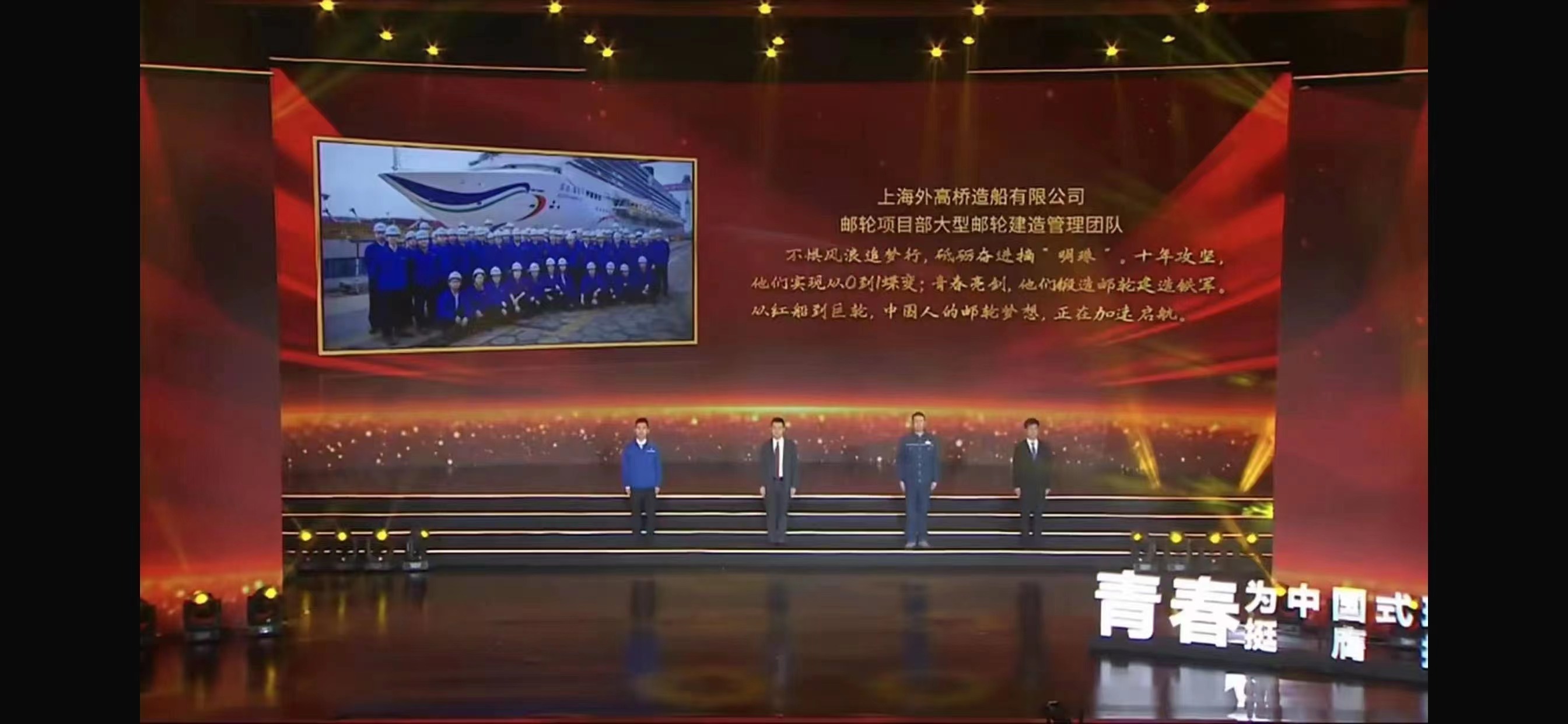
The large cruise ship construction management team of the Cruise Project Department of Shanghai Waigaoqiao Shipbuilding Co., Ltd. won the 28th "China Youth May Fourth Medal Group".
"(But) if you have the opportunity to see it, the cruise ship is densely packed with pipelines and lines. How to put all the necessary systems in this relatively narrow space requires very high layout of the entire system, pipelines and circuits. It is very difficult to lay out more than 4,700 kilometers of cables. This is just one of the problems. The space is limited, and two completely independent systems must be set up to ensure redundancy - when one system fails, the other must be able to take over." said Nie Kai.
The third problem is vibration and noise. Cruise ships emphasize the comfort of tourists, and each room and each public area has strict requirements for noise control. There are more than 2,000 rooms and many public areas on Cruise Ship No. 1. The six sides of a closed space, including top, bottom, left, right, front and back, are all equipped with sound insulation materials to isolate noise. However, any simple problem may become more difficult to solve after multiplying it by 2,000.
Despite so many difficulties, on November 4, 2023, China's first domestically-produced large cruise ship "Aida Modou" was officially named and delivered.
On January 1, 2024, the cruise ship started its first commercial voyage, which lasted seven days and six nights, from Shanghai to Jeju, South Korea, Nagasaki and Fukuoka, Japan, with a distance of 1,119 nautical miles.
On January 7, it brought more than 3,000 tourists safely back to Shanghai Wusongkou International Cruise Port.
Take the factory as home: pioneering youth, dedicated youth, innovative youth, and youth who dare to challenge
"I volunteered to come here and asked to be able to gain experience in a large project. This is a large project that I could never have imagined before."
Nie Kai is one of the first employees of the cruise project department, the engineering command department of the first domestically-made large cruise ship. In 2019, this project department had only 16 people. He is the first backbone force, and there are many difficult problems waiting for him to "chew".
Earlier, in 2014, Nie Kai joined a subsidiary of Waigaoqiao Shipbuilding, working in the front-line production department of Shanghai Lingang. In 2018, when he heard that the cruise ship project was about to start construction, he applied to participate.
Nie Kai said, "I can do well in my comfort zone, but I am willing to accept new challenges, which is also a characteristic of young people today."
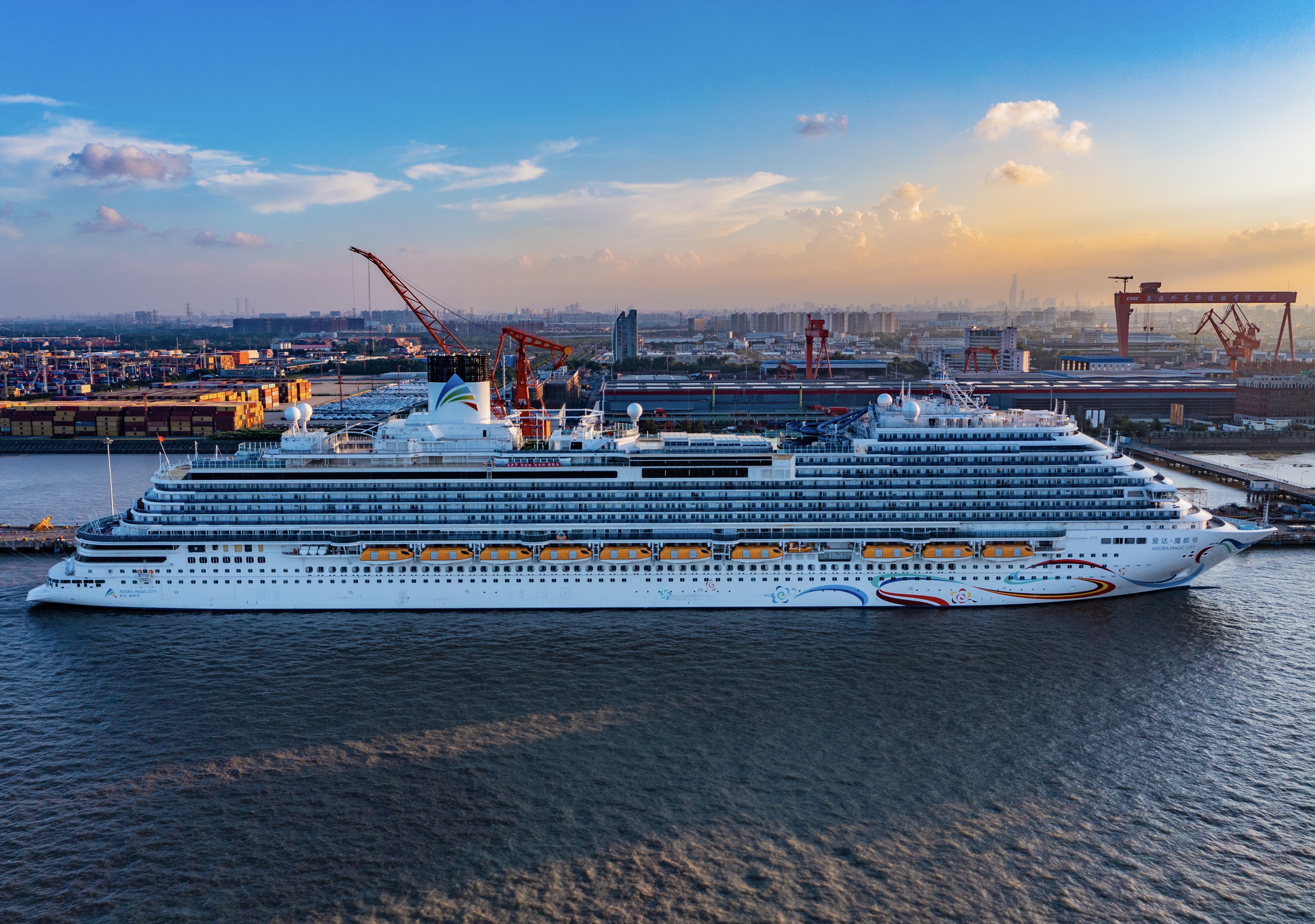
The first large cruise ship built in China, the Aida Modou.
"Since I started working on the cruise project, I have always had this feeling: the more you know, the more you need to know. Otherwise, you may not be able to communicate with others. You need to understand design, procurement, construction, debugging, and finally, after-sales. Then, you will have a more comprehensive understanding of the overall situation and it will be easier to work," he said.
From scratch, the cruise project was on track in 2020. Nie Kai was in charge of the turnkey management of the cruise project, which involved 102 engineering packages, a scale that was unprecedented in the history of Chinese shipbuilding. He conducted in-depth research on the management process, implemented each project, and ensured the smooth completion of the cruise project.
At the same time, as the secretary of the Youth League branch of the cruise project, Comrade Nie Kai set an example himself, set a positive role model for young league members, communicated and held discussions with young employees in a timely manner, and helped solve problems.
Ma Yulin joined the company in 2012 and worked in the shipbuilding department and other front-line departments. In 2018, he served as the company's Youth League Committee Secretary. He said, "There are many young people in the factory, more than 1,000 league members, and about 3,000 young people under the age of 35. Young people should be trained in large projects and grow in the projects."
"I also want to challenge new projects!" Ma Yulin said. The temperature on the deck is relatively high in summer, and they also have to be on site. They eat and live in the factory and regard the factory as their home.
In order to ensure the timely and high-quality delivery of the first domestically-made large cruise ship, the team organized and planned carefully, coordinated and implemented policies rigorously, and promoted the construction of a cruise ship construction system framework of "production planning capability construction with construction as the core". Through the management and control of production preparation, production planning, advance construction, outfitting construction, follow-up construction, completion management and other aspects, Waigaoqiao Shipyard's cruise ship construction system was gradually established; innovative engineering general contractor managers, regional managers, and system managers were established to meet the work needs of the site at different time periods.
After the delivery of the first cruise ship, the team organized and compiled various summaries and management manuals to record the management experience of the first cruise ship and retain valuable experience for the construction of subsequent cruise ships.
By the end of 2023, the first domestically-produced large cruise ship has successfully completed major milestones such as launching, sea trials, naming and delivery, and three navigation guarantees this year, achieving a major breakthrough in my country's cruise ship research and development. my country has become the sixth country in the world to successfully design and build large cruise ships, and it is also the first country in the world that has the ability to design and build the "three pearls" of the shipbuilding industry.